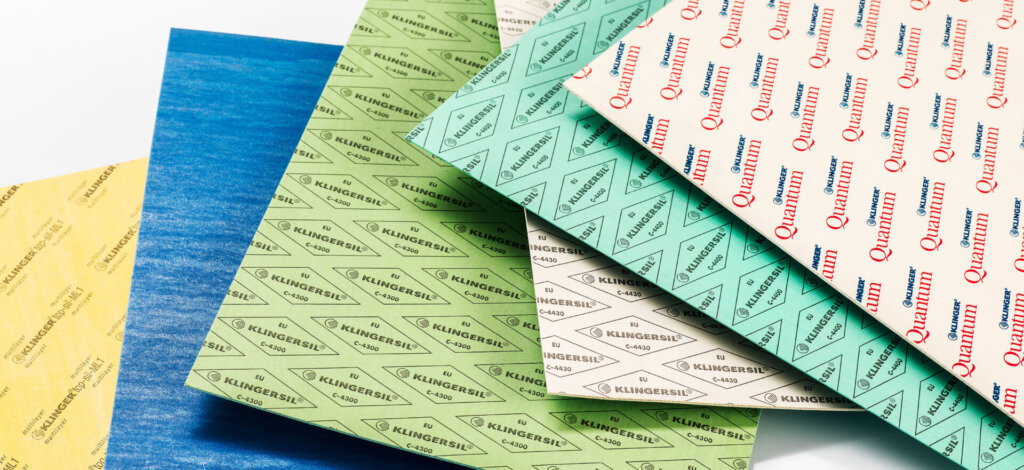
When we talk about sealing and fluid control systems, safety, durability, and efficiency are some of the key factors. To achieve results that deliver on these aspects, we must first and foremost understand which solution to use.
At KLINGER Portugal, we know there is no one-size-fits-all answer, and that with the vast range of available seals and gaskets, it can be difficult to find the ideal one. Each application requires a technical and thorough approach, with different steps to follow.
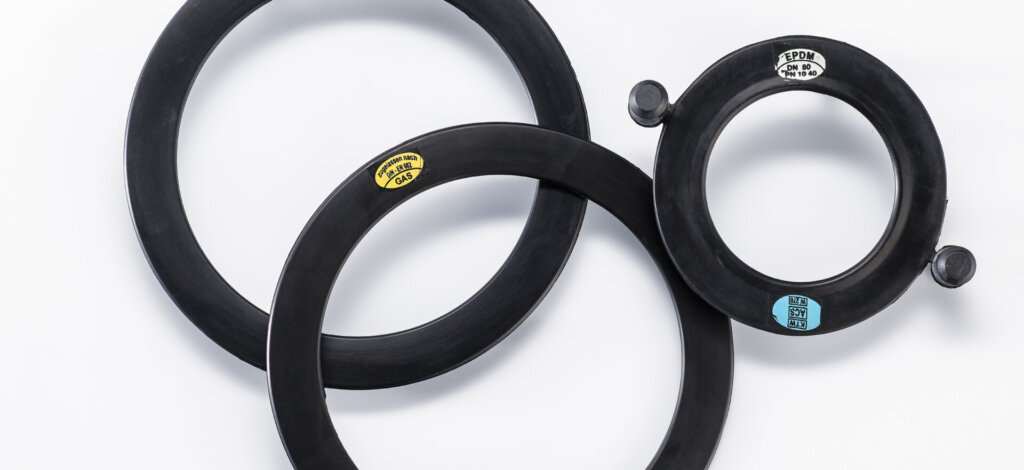
Before beginning any kind of selection, it is necessary to compare the most commonly used materials:
» Fibres: Industrial fibres are composite materials designed for applications requiring resistance to high temperatures, chemical aggressiveness, and intense mechanical loads. Their customised combinations (cellulose, aramid, carbon, glass) vary depending on technical requirements.
» PTFE (Polytetrafluoroethylene): A material with high chemical resistance, ideal for aggressive environments and high temperatures (up to 260°C), but not suitable for extremely high pressures.
» Graphite: With excellent thermal conductivity, it withstands very high pressures and temperatures (up to 500°C in inert atmospheres). Ideal for harsh industrial environments.
» Mica: With internal reinforcement in perforated stainless steel, designed to withstand continuous temperatures up to 900°C, it is ideal for applications with intense dry heat and low pressure (up to 5 bar).
» Rubber (NBR, EPDM, FKM, etc.): Economical and versatile, easily adaptable to different types of fluid. It is important to select the correct rubber according to fluid compatibility and temperature. (e.g., EPDM for steam, FKM for hydrocarbons and chemicals).
» Semi-Metallic: Designed for applications where pure metals or non-metallic materials are not sufficient, semi-metallic gaskets (SWG) stand out for their sealing capability under extreme conditions. Combining the durability of metal with the adaptability of GRAPHITE/PTFE, they ensure long-lasting tightness, even in systems with cyclical start-ups and shutdowns.
» Metallic: Manufactured from high-performance alloys (such as Stainless Steel, Titanium, or Inconel), they are designed to withstand extreme pressures (up to 1,500 bar), resist critical temperatures (-200°C to 800°C), provide sealing in corrosive environments, and absorb thermal expansion.
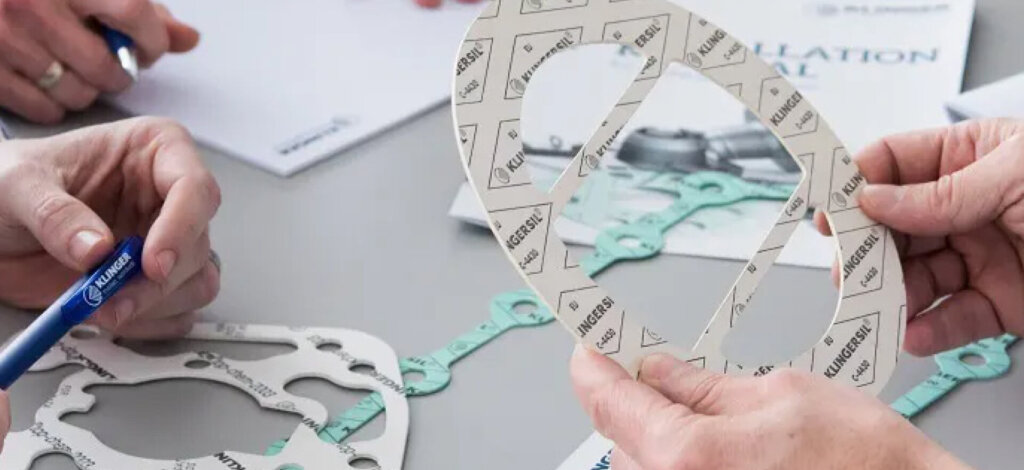
This selection process, however, is not just about distinguishing the materials. It also requires careful consideration of the following factors:
» Temperature: It is essential to maintain the material’s mechanical properties. Some may harden, soften, or degrade, so the right material must be chosen for the operating temperature.
» Pressure: It is crucial to select seals and gaskets that can withstand the system’s pressure without deformation.
» Fluid: The material must be chemically resistant to the fluid being used. Otherwise, degradation, corrosion, and failure may occur.
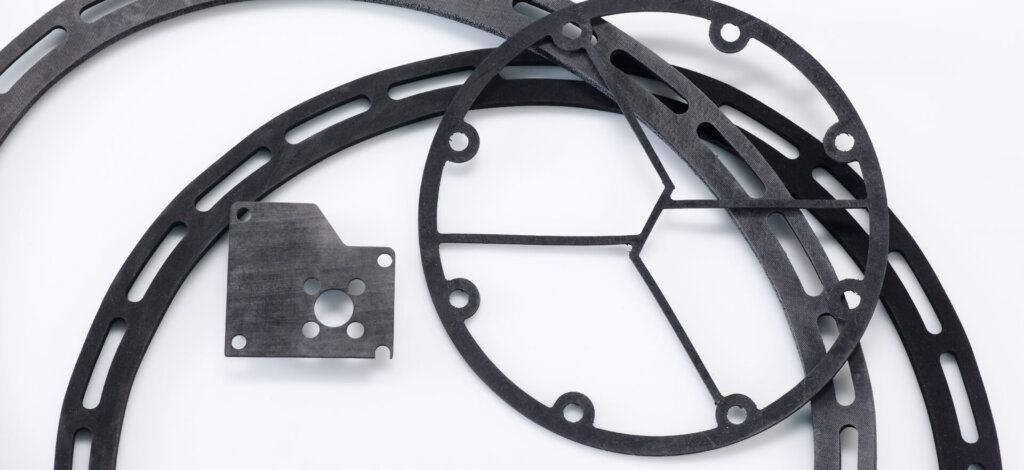
The correct choice of material has a direct impact on system efficiency, leakage reduction, and operational safety. Inadequate materials can compromise the installation’s operation and lead to unwanted downtime and high costs. At the same time, they may also be the cause of workplace accidents.
At KLINGER Portugal, we help you identify the most effective solution for each type of application, taking all necessary factors into account. Our goal is to ensure that every system operates at the highest quality—today and in the future.
For more information, please contact our team.